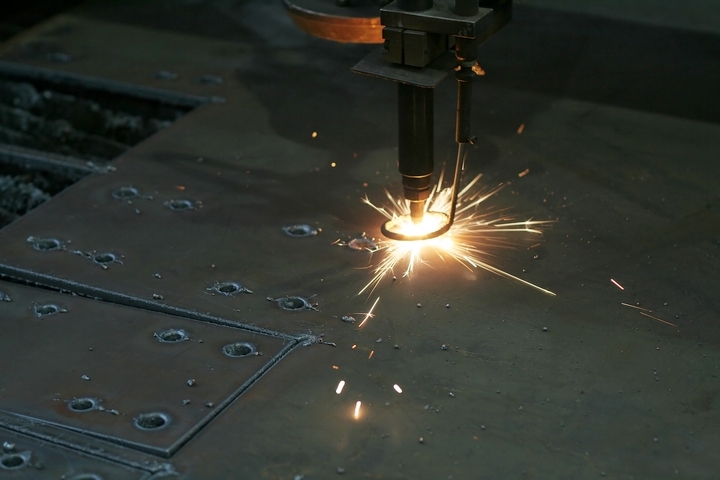
Sheet metal is a thin metal that comes in large pieces – sheets. It is one of the most versatile materials for building and creating things. As such, with all of the methods and tools that have been developed for sheet metal fabrication, it is possible to build or create almost anything out of sheet metal.
1. It is done in steps
Sheet metal fabrication is done in a series of steps which include cutting the big sheet metal down to size, cutting out the necessary pieces, forming them, and attaching those pieces together. The final step is to sand down and paint or decorate the item to look nicer. There may be multiples of each step, depending on the item being made, or some steps may be left out if they are unnecessary for a project.
2. There are many thicknesses
Although sheet metal is considered a thin metal, there are different thicknesses. Depending on the material, sheet metal can range, for example with standard steel, from about 6 millimetres down to about .15 millimetres in thickness. Other materials come in varying thicknesses, but do not generally thicker than about 14 millimetres.
3. There are many cutting methods
Because there are so many different materials that can be used for sheet metal, and because of the different thicknesses, having cutting methods that are better for certain qualities is necessary. For instance, snipping sheet metal with “tinsnips” is a good cutting method for softer, thinner metals, while plasma cutting can handle a thicker, harder metal. Other methods of cutting include: punching or blanking, the method of punching pieces out of a larger piece; water jet cutting which uses a blast of water to cut materials; and laser cutting which uses a laser to cut the materials. Each has their strengths and weaknesses for cutting different materials and thicknesses.
4. Lots of metals can be sheet metal
Part of what makes sheet metal so versatile is that so many metals can be made into sheet metal. Standard steel, galvanized steel, copper, silver, gold, platinum, brass, aluminum, tin, nickel, titanium, zinc, and more can all be turned into sheet metal. Different metals have different properties which make them easier or harder to work with on certain projects. For instance, stainless steel is much heavier than aluminum, but aluminum is harder to weld than stainless steel. So depending on the item you plan to create, you may have to choose a different material that will work with you rather than against you.
5. The cut is not always perfect
Depending on the cutting method used, the piece may have what are often called burrs. These are rough edges left after a piece has been cut. These can be sharp and dangerous, and are not really acceptable for a final product. Luckily, there are methods to remove these burrs. Deburring can be done by hand with a special tool; thermal deburring is a method used where pieces are put into a sealed chamber and the burrs are burned away; barrel tumbling is where all pieces are put together in a barrel that moves around causing the pieces to essentially deburr themselves by rubbing against each other.
6. It is used in almost every industry
Sheet metal fabrication and its methods are used in almost every industry. From the transportation industry where sheet metal is used in the construction of planes and cars to the architectural industry where sheet metal can be used in buildings and even into the medical industry where sheet metal is used for surgical tables, sheet metal touches almost every area of our lives in some way or another.